I am using a 4″ x 36″ stationary sander from Harbor Freight to grind with. I did some minor modifications to it to make it easier to use. These can be found on sale fairly regularly for about $60. I removed the belt guards and the tool rest because to change a belt they have to be removed. As you work on grinding out a knife you will need to switch belts for the appropriate grit and as they wear out. I also added a bar to hold the grinder in place on the workbench so it doesn’t slide around when grinding.
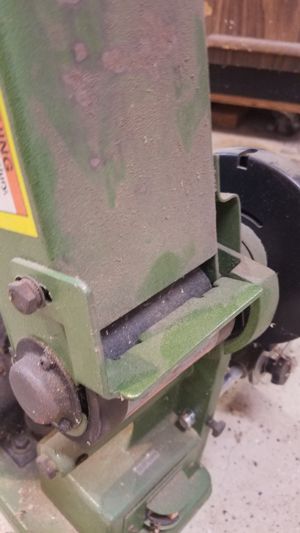
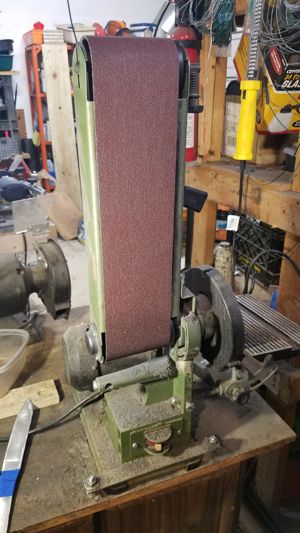

I started by using the 80 and 120 grit belts available from Harbor Freight. Somewhere I picked up some 40 grit belts as well. They will remove stock but it takes a long time. I still use Harbor Freight 80 grit belts for initial shaping of the handle or any other task where I don’t want to damage or put extra wear on my “good” belts. I found some Zirconia belts from Red Label Adhesives that last longer and are available in coarser grits but of course cost more. I use the 24 grit belt for rough metal stock removal. As the grinding process continues work my way through the other grits (typically 40 and 80) as the blade gets closer to being ready for hardening.
It takes more time than desirable using this setup. It cannot remove material anywhere near as fast as most 2″ x 72″ grinders. The lack of different sized pulley wheels makes hollow grinding almost impossible. The only spot to attempt a hollow grind is using one of the ends of the grinder but free-handing without a work piece rest requires a very steady hand.
Deciding how much material to leave prior to hardening can be difficult (at least for me). All of the hammer marks should be ground out at this stage. You want to remove as much stock as possible to reduce the grinding time after tempering, however you need to leave enough meat on the knife to prevent warping during the quench. This is less of an issue if you are edge quenching versus quenching the entire blade.
After the blade is hardened and then tempered I will go back to the grinder and grind with 80, 120, 220, and 400 grit belts.